Robotics Welding Market Analysis
Based on type, the market is segmented into arc welding and spot welding, MIG (Metal Inert Gas), TIG (Tungsten Inert Gas), laser welding and others. The spot-welding segment dominated the market in 2022, accounting for a revenue of over USD 2.1 Billion in 2022; this segment is also estimated to register a CAGR of about 12% over the forecast period.
- Spot welding is a fast & highly efficient welding process. The robots equipped with spot welding tools can perform welds quickly & consistently, leading to increased productivity in manufacturing processes. This efficiency is especially valuable in industries with high production volumes.
- Robotic spot welding ensures a consistent & high-quality weld on all occasions. Robots are programmed to follow precise welding parameters, which helps in reducing the likelihood of defects or errors in the welding process. This consistency is crucial in industries, such as automotive and aerospace, where the weld quality is critical.
- With significant initial investments in robotics welding systems, the long-term cost savings can also be substantial. Robots can operate continuously, thereby reducing labor costs and minimizing the downtime associated with human workers. The automation of spot welding can also lead to material savings due to optimized welding patterns and reduced waste generation.
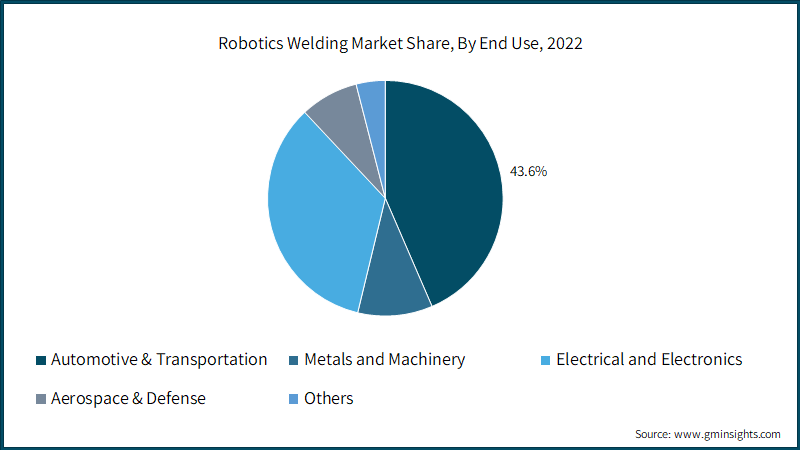
Based on end use, the robotics welding market is segmented into automotive & transportation, metals & machinery, electrical & electronics, as well as aerospace & defense. The automotive & transportation segment held a business share of over 8.4% in 2022 and is estimated to grow over the forecast period.
- Automotive manufacturing requires high precision & consistency in welding processes. Robotics welding systems excel in providing accurate & repeatable welds, ensuring the quality of the final product. Robots can work continuously without breaks, leading to increased production efficiency. This is crucial in the automotive industry, where high production volumes are common.
- The automotive industry is embracing Industry 4.0 principles, which include the integration of automation, data exchange, and smart technologies. Robotics welding systems can easily be integrated into these smart manufacturing environments.
- The automotive industry is under increasing pressure to reduce emissions and improve fuel efficiency. As a result, manufacturers are exploring lightweight materials such as aluminum, which require precise welding. Robotics welding can effectively handle these materials.
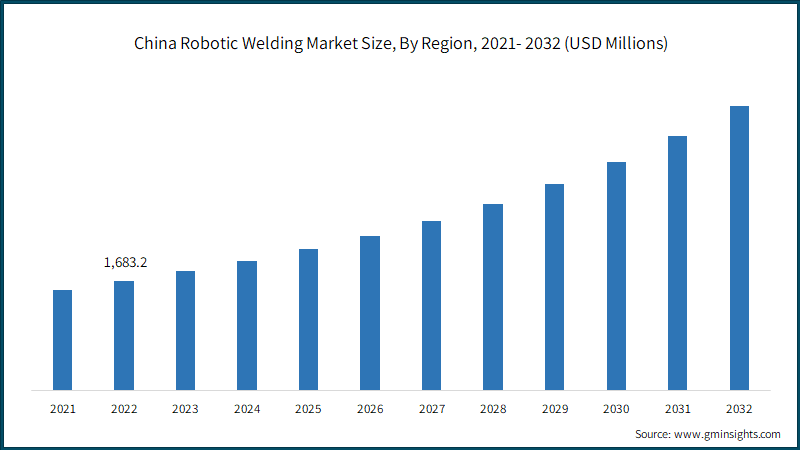
Asia Pacific led the robotics welding market in 2022, accounting for a significant market share of over 10.5%. The Asia Pacific region is experiencing significant growth in the market due to rapid industrialization, the rising demand for automation solutions, and the need for cost-effective labor alternatives. Manufacturers in the region are increasingly adopting robotics welding solutions to enhance productivity and maintain consistent weld quality. The availability of skilled labor, coupled with the government initiatives promoting automation, is driving market trends. The growing automotive and construction sectors in Asia Pacific are fueling the demand for efficient & precise welding processes, leading to the market growth in the region.