Home > Construction > Construction Equipment > Carbide Tools Market
Carbide Tools Market Size
The global carbide tools market was valued at USD 12.9 billion in 2023 and is estimated to grow at a CAGR of over 3.9% from 2024 to 2032. As the manufacturing landscape increasingly embraces automation and robotics, the demand for high-precision carbide tools, adept at thriving in high-speed automated settings, is surging.
This demand is especially evident in CNC machining and robotic assembly lines. A notable trend is the advancement of coatings such as diamond-like carbon (DLC), titanium nitride (TiN), titanium carbonitride (TiCN), and aluminum titanium nitride (AlTiN). These innovative coatings bolster the wear resistance of carbide tools while simultaneously boosting their thermal stability and resistance to oxidation.
Report Attributes | Details |
---|---|
Base Year: | 2023 |
Market Size in 2023: | USD 12.9 Billion |
Forecast Period: | 2024 – 2032 |
Forecast Period 2024 – 2032 CAGR: | 3.9% |
2024 – 2032 Value Projection: | USD 17.3 Billion |
Historical Data for: | 2021-2023 |
No. of Pages: | 220 |
Tables, Charts & Figures: | 180 |
Segments covered: | Product Type, Coating Type, Application, End-Use and Region |
Growth Drivers: |
|
Pitfalls & Challenges: |
|
Carbide Tools Market Trends
There's a rising demand for customized carbide tools, specifically tailored to meet the unique needs of various industries. Manufacturers are on the lookout for tools that cater to specialized applications, be it intricate mold-making or working with specialized materials like ceramics, composites, and titanium alloys. Notably, the automotive sector stands out as a primary consumer of carbide tools. This demand is further amplified by the burgeoning electric vehicle (EV) market and a pronounced shift towards lightweight materials, including aluminum and carbon fiber composites.
Carbide Tools Market Analysis
Smart manufacturing systems are transforming with the integration of Internet of Things (IoT) technology, particularly in the utilization of carbide tools. These tools now come equipped with sensors that monitor wear, performance, and temperature in real-time. As sustainability gains prominence in manufacturing, there's a noticeable shift towards eco-friendly practices in tool production. Additionally, there's an intensified focus on recycling carbide and minimizing the carbon footprint in the manufacturing processes of carbide tools.
Carbide tools, crafted from tungsten carbide, come at a premium compared to tools made from other materials. This elevated cost poses challenges for small and medium-sized enterprises (SMEs) with tighter budgets, particularly in cost-sensitive industries. Furthermore, the production of carbide tools hinges on the availability of raw materials, notably tungsten. Consequently, fluctuations in the raw material market can sway the production costs of carbide tools, subsequently influencing the market's growth trajectory.
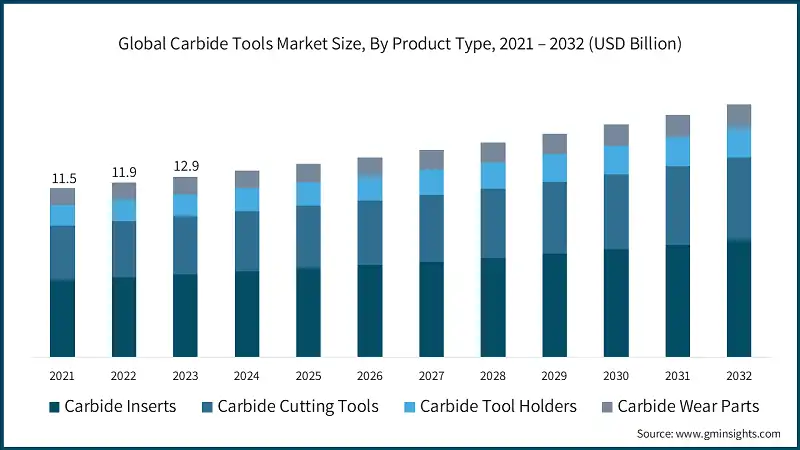
Based on product type, the carbide inserts segment was worth around USD 5.6 Billion in 2023 and is estimated to grow at a CAGR of over 4% from 2024 to 2032. Tungsten carbide, renowned for its exceptional hardness, wear resistance, and high-temperature endurance, is the primary material used in carbide inserts. These attributes markedly elevate the performance of cutting tools, enabling them to operate at increased speeds, achieve enhanced precision, and extend their lifespan before requiring replacement. As the demand for high-precision manufacturing surges across various sectors, industries with stringent component tolerances, like medical devices and electronics, are particularly benefiting. This precision, facilitated by carbide inserts, is propelling their widespread adoption and subsequently fueling the market growth.
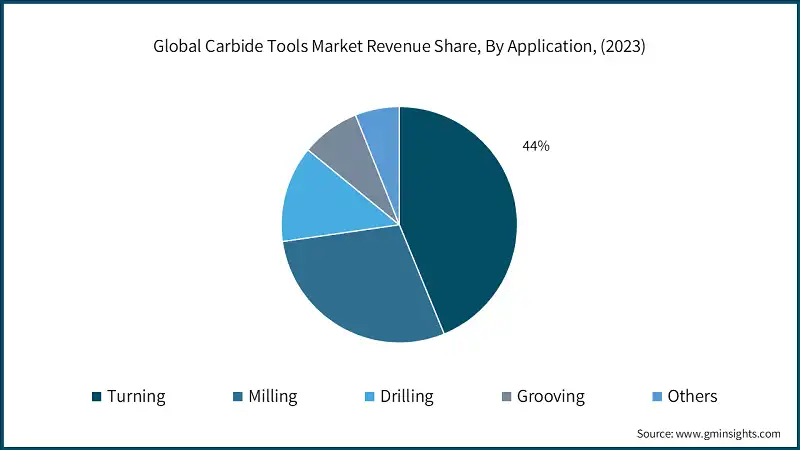
Based on the application, the turning segment held around 44% of the market share in 2023 and is anticipated to grow at a CAGR of 4.1% through 2032. Industries such as aerospace, automotive, medical device manufacturing, and electronics, which demand high-precision machining, rely heavily on turning applications. Carbide tools, known for their exceptional hardness and wear resistance, excel in precision turning. They consistently deliver high-quality finishes, even on challenging materials like stainless steel, titanium, and superalloys.
A key driver for the adoption of carbide tools in turning operations is their capability to maintain performance and precision at elevated cutting speeds. This advantage allows manufacturers to boost production rates, shorten cycle times, and enhance overall efficiency, leading to a heightened demand for carbide tools.
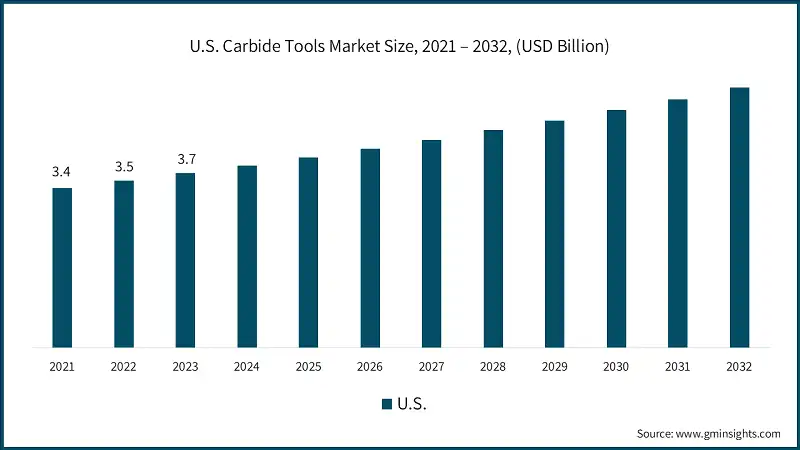
U.S. region dominated 78% share of the carbide tools market in 2023. Several high-demand industries in the U.S., including aerospace, automotive, medical devices, electronics, and energy sectors, heavily rely on carbide tools for manufacturing and precision machining. As these industries increasingly demand customized carbide tools, U.S. companies are investing in innovative solutions tailored to these specialized needs.
Country-level Analysis
North America: U.S. manufacturers are developing advanced coatings, including TiN and AlTiN, alongside innovative carbide alloys, to boost the performance and longevity of carbide tools. These advancements are fueling the growth of the carbide tools market in North America, addressing the rising demands for high-speed and high-precision manufacturing. Furthermore, the reshoring of vital manufacturing sectors, especially in high-value domains such as aerospace and medical devices, is amplifying the demand for carbide tools. This surge is driven by companies' aspirations to enhance production efficiency and uphold stringent quality standards.
Europe: In Germany's automotive sector, the demand for carbide tools is robust, driven by the need for precision machining of high-performance materials like aluminum alloys, composites, and steel. With the automotive industry pivoting towards electric vehicles (EVs) and lightweight designs, there's an escalating need for specialized tools adept at machining complex and hard materials. Germany boasts some of the world's premier automotive manufacturers, including Volkswagen, BMW, Mercedes-Benz, and Audi. Additionally, the nation hosts a strong industrial machinery sector, featuring companies such as Siemens and DMG Mori. Both these industries are heavily dependent on high-precision cutting tools for crafting automotive parts, machinery, and components.
Asia Pacific: China's construction and heavy machinery sectors are increasingly demanding carbide tools. This surge is driven by the need for high-performance tools adept at machining the high-strength materials prevalent in construction equipment. Chinese manufacturers, increasingly integrating CNC machines and automation systems, are driving up the demand for precise and durable cutting tools. With China's ongoing embrace of Industry 4.0 technologies, there's a surging demand for carbide tools. These tools are essential to endure the heightened speeds, temperatures.
Middle East: In Saudi Arabia, the burgeoning steel production and machinery manufacturing sectors are increasingly dependent on high-quality carbide tools for operations such as turning, milling, and drilling of tough materials. These carbide tools, especially drills, inserts, and cutting tools, play a pivotal role in downhole drilling, pipeline construction, and refinery maintenance. With the nation's ongoing investments in oil exploration, offshore drilling, and advanced refining technologies, the demand for robust carbide tools capable of withstanding these rigorous applications is on the rise.
Carbide Tools Market Share
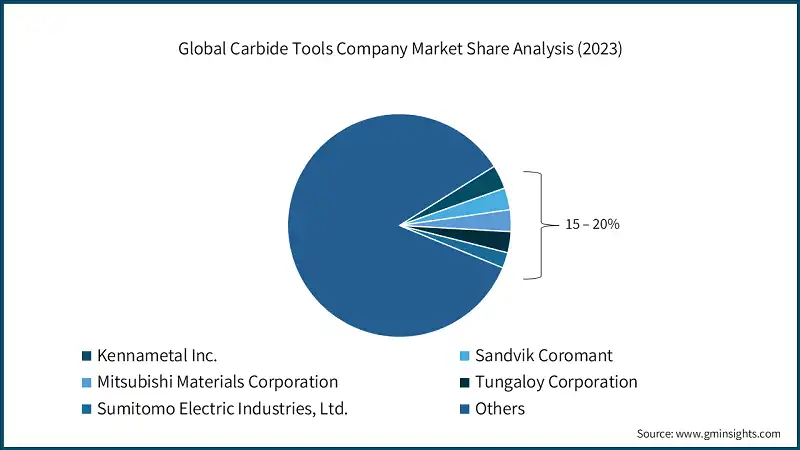
The global market for carbide tools showcases a competitive landscape teeming with a mix of players, from multinational giants to regional manufacturers and specialized niche companies. Predominantly fragmented, the market sees major players like Kennametal Inc., Sandvik Coromant, Mitsubishi Materials Corporation, Tungaloy Corporation, Sumitomo Electric Industries, Ltd. These companies command significant market shares, bolstered by their vast product portfolios and robust brand recognition. The surge of e-commerce has broadened online sales channels, allowing brands to tap into wider audiences and boost customer engagement via digital marketing.
Carbide Tools Market Companies
Major players operating in the carbide tools industry are:
- Carbide Tool Solutions
- Ceratizit Group
- Gühring KG
- Hitachi Tool Engineering, Ltd.
- Iscar Ltd.
- Kennametal Inc.
- Kyocera Corporation
- Mitsubishi Materials Corporation
- OSG Corporation
- Sandvik Coromant
- Seco Tools
- Sumitomo Electric Industries, Ltd.
- Tungaloy Corporation
- Walter AG
- ZCC Cutting Tools
Carbide Tools Industry News
- In October 2024, Kennametal Inc. expanded its turning product line, introducing new inserts and cutting tools tailored for small parts and medical machining. The newly launched TopSwiss Turning Inserts, Micro Boring Solid (MBS) tooling, and KCU25B Turning Inserts are designed to enhance productivity, elevate component quality, reduce errors, and ensure customers attain precise and clean machining outcomes.
- In May 2024, Mitsubishi Materials Corporation (MMC) marked a significant milestone in its global manufacturing strategy by completing the expansion of its Cemented Carbide Tool Plant in Valencia, Spain. This expansion directly addresses the surging demand for high-performance cutting tools across industries like automotive, aerospace, and general manufacturing. It underscores MMC's dedication to delivering innovative, precision-engineered solutions to its worldwide clientele.
This carbide tools market research report includes in-depth coverage of the industry with estimates & forecast in terms of revenue (USD Million) & volume (Thousand Units) from 2021 to 2032, for the following segments:
Click here to Buy Section of this Report
Market, By Product Type
- Carbide Inserts
- Carbide Cutting Tools
- Carbide Tool Holders
- Carbide Wear Parts
Market, By Coating Type
- PVD (Physical Vapor Deposition) Coated
- CVD (Chemical Vapor Deposition) Coated
- TiN (Titanium Nitride) Coated
- Uncoated
- Others (Titanium Aluminum Nitride Coated, Etc)
Market, Application
- Turning
- Milling
- Drilling
- Boring
- Threading
- Others (Grooving Inserts, Etc)
Market, End-Use
- Automotive
- Aerospace & Defense
- Construction
- Machinery Manufacturing
- Oil & Gas
- Power Generation
- Others (Mining, Medical Equipment Manufacturing, Etc)
The above information is provided for the following regions and countries:
- North America
- U.S.
- Canada
- Europe
- UK
- Germany
- France
- Italy
- Spain
- Russia
- Asia Pacific
- China
- India
- Japan
- South Korea
- Australia
- Latin America
- Brazil
- Mexico
- MEA
- UAE
- Saudi Arabia
- South Africa
Frequently Asked Questions (FAQ) :