Home > Automotive > Automotive Materials > Metals > Automotive Casting Market
Automotive Casting Market Size
Automotive Casting Market size was valued at USD 72.03 billion in 2023 and is anticipated to register a CAGR of 5.8% between 2024 and 2032. Increasing automotive production drives the market growth. Global vehicle demand is rising due to population growth and urbanization, especially in developing countries. Economic growth in markets like China, India, and Brazil has led to more vehicle production to meet domestic demand. As living standards improve, more consumers can afford vehicles.
The automotive industry is investing in plant expansions and new technologies, such as automation and robotics, to increase production efficiency and capacity. Government policies and incentives that support manufacturing are also boosting automotive production. These factors are increasing the demand for automotive castings, which are essential in vehicle manufacturing.
Report Attributes | Details |
---|---|
Base Year: | 2023 |
Market Size in 2023: | USD 72.03 Billion |
Forecast Period: | 2024 – 2032 |
Forecast Period 2024 – 2032 CAGR: | 5.8% |
2024 – 2032 Value Projection: | USD 119.16 Billion |
Historical Data for: | 2021 - 2023 |
No. of Pages: | 135 |
Tables, Charts & Figures: | 49 |
Segments covered: | By material, Process, application, distribution channel, vehicle |
Growth Drivers: |
|
Pitfalls & Challenges: |
|
Government regulations to reduce vehicle emissions are pushing automakers to use lightweight materials and efficient manufacturing processes. According to the Environmental Protection Agency (EPA), vehicles that use lightweight materials can improve fuel efficiency by up to 20%. To meet these standards, manufacturers are increasingly using materials like aluminum and magnesium for casting, which help reduce vehicle weight and improve fuel efficiency.
Advanced casting techniques, such as high-pressure die casting and precision sand casting, allow for the production of complex, high-strength components that enhance vehicle efficiency and performance. This trend not only helps automakers comply with regulations but also drives innovation and growth in the market.
The high cost of casting materials presents a major challenge in the automotive casting market. Lightweight metals like aluminum and magnesium are more expensive than traditional steel due to factors such as mining, processing, and global demand. Advanced composites like carbon fiber, which offer better strength-to-weight ratios, are even more costly because of their complex manufacturing processes and high raw material costs. Additionally, the specialized equipment needed for casting these materials, such as high-pressure die casting machines, further increases expenses due to high purchase, maintenance, and operational costs.
Automotive Casting Market Trends
The automotive casting industry is being significantly reshaped by the surge of electric vehicles (EVs). With the escalating demand for EVs, manufacturers are homing in on crafting specialized cast components, tailored specifically for electric powertrains. These components, spanning from battery housings to motor casings and structural parts, are increasingly being fashioned from lightweight and efficient materials. The emphasis on materials like aluminum and magnesium is especially pronounced in EVs, given their direct impact on both battery efficiency and driving range through weight reduction.
Furthermore, the ascent of EVs is spurring casting technology innovations, notably in high-pressure die casting and precision sand casting. These advancements are enabling the production of intricate, high-performance components with heightened precision and reduced production costs. This drive for sustainability and eco-friendliness in vehicles dovetails with the broader casting industry's trend towards recyclable and energy-efficient materials and processes. With automakers channeling significant investments into EV production and infrastructure, the demand for cutting-edge casting solutions is poised to surge, underlining the pivotal role of EVs in shaping the future of the market.
Automotive Casting Market Analysis
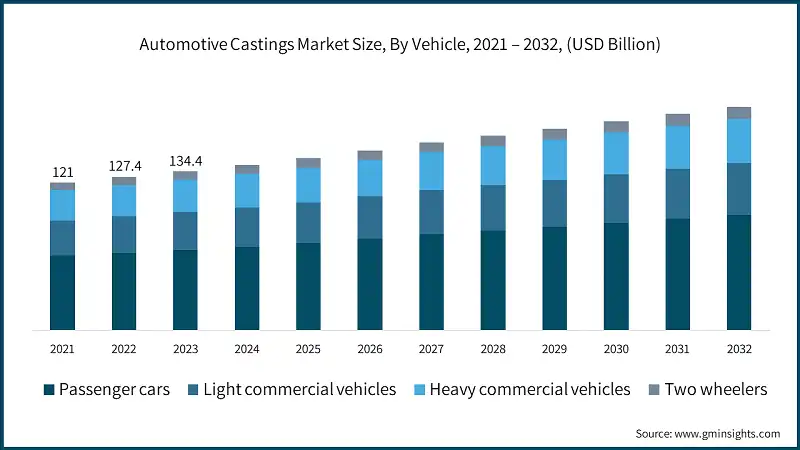
Based on vehicle type, the market is segmented into Passenger cars, Light commercial vehicles, Heavy commercial vehicles and Two wheelers. In 2023 passenger cars dominated the market generating a revenue exceeding USD 65 billion and is expected to reach more than USD 105.1 billion by 2032. Passenger vehicles lead the automotive casting market due to their high production volumes and strong consumer demand. The large-scale production of passenger cars drives significant demand for cast components like engine blocks, transmission cases, and structural parts. This segment is quick to adopt advanced casting technologies and materials, driven by consumer preferences for better performance, fuel efficiency, and safety.
Strict regulations on fuel efficiency and emissions also push the need for innovative casting solutions. Additionally, the passenger vehicle market benefits from ongoing customization and frequent model updates, which create a continuous need for specialized cast components. The steady aftermarket demand for replacement parts and repairs further strengthens the dominance of passenger vehicles in the casting market. These factors collectively make the passenger vehicle segment a key driver of growth and innovation in the market.
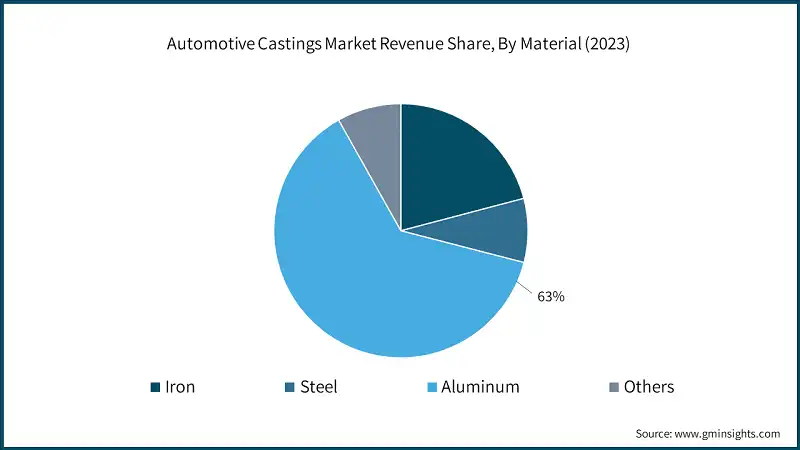
Based on material type the automotive casting market is segmented as Iron, steel, aluminum and others. The aluminum material emerged as the dominant segment holding a market share of 63% and is anticipated to grow at a CAGR of 5.8% through 2032. Aluminum leads the market due to its lightweight, which reduces vehicle weight and improves fuel efficiency. This aligns with the industry's focus on sustainability and stricter environmental regulations. Its high strength-to-weight ratio ensures durability and safety, while its corrosion resistance increases the lifespan of automotive parts.
Aluminum's flexibility allows for casting complex shapes, making it ideal for innovative automotive components. Additionally, its excellent recyclability supports the industry's goal of reducing environmental impact. Despite a higher initial cost, aluminum's benefits in fuel savings and durability, along with advancements in casting technologies, make it prevalent in the market.
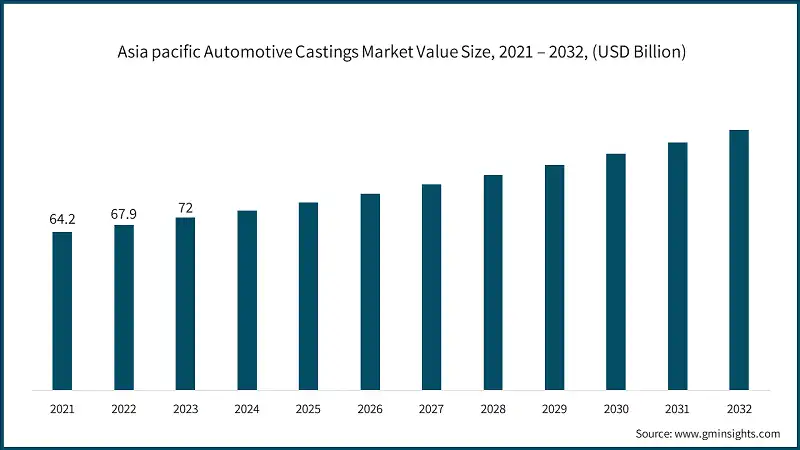
Asia pacific automotive casting market size dominated around USD 72 billion in 2023 and is expected to reach USD 119.16 billion by 2032. Rapid industrialization and urbanization in countries like China and India have increased vehicle production and demand. The region's strong automotive manufacturing base, supported by many original equipment manufacturers (OEMs) and suppliers, drives market growth.
Additionally, Asia-Pacific countries are investing heavily in technology and infrastructure, enhancing their casting capabilities. Lower labor and production costs also give the region a competitive edge. Government policies and incentives to boost the automotive sector, along with a focus on producing lighter and more fuel-efficient vehicles, further strengthen Asia-Pacific's dominance in the market.
North America: The U.S. dominated the North America automotive casting market with a share of 84.29% and is anticipated to grow at a CAGR of 5.4% during the forecasted period. This dominance is due to the region featuring major manufacturers and suppliers. This strong industry drives high demand for casting components needed in vehicle production. The region benefits from a well-established supply chain and advanced manufacturing capabilities, ensuring efficient production and distribution of these components. Continuous growth and innovation in the automotive sector increase the need for high-quality casting solutions to meet changing demands.
Europe: Germany led the Europe automotive casting market with a revenue of around 27.66% and is anticipated to grow at a CAGR of 5.2% during the forecasted period. Germany is a global leader in automotive manufacturing, with major OEMs like Volkswagen, BMW, and Mercedes-Benz. This strong automotive sector drives high demand for advanced casting solutions, especially for high-performance and precision-engineered components. The country's focus on innovation, strict environmental regulations, and the shift towards electric vehicles further increases the need for advanced casting materials. With its emphasis on sustainability and manufacturing excellence, Germany remains a key player in the market, supporting the development of high-quality, efficient, and eco-friendly automotive components.
Asia Pacific: China dominated the Asia Pacific automotive casting market with a market share of 54.58% and is anticipated to grow at a CAGR of 6.6% during the forecast period. China's government is promoting electric vehicles (EVs) through subsidies and policy support. This shift to EVs increases the need for lightweight components to improve battery efficiency and vehicle performance, driving demand for aluminum and other lightweight castings. This focus on EVs aligns with China's environmental goals and supports the growth of advanced casting technologies needed for high-performance, energy-efficient components.
Automotive Casting Market Share
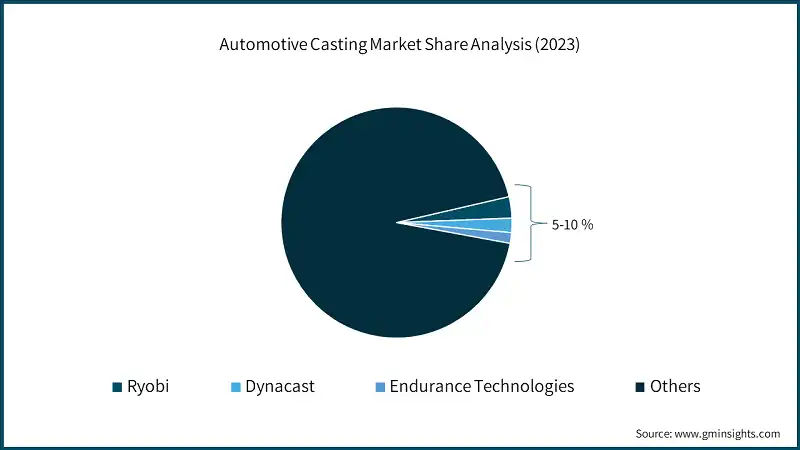
The automotive casting industry has prominent players, such as Ryobi, Dynacast and endurance technologies holding a market share of 5-10%. Manufacturers are adopting strategic steps, such as mergers, acquisitions, partnerships, and collaborations, to meet the growing consumer demand and consolidate their position in the market.
Automotive Casting Market Companies
Major players operating in the automotive casting industry include:
- Bell Foundry
- Buhler AG
- CFS Foundry
- Dawang Steel Castings
- Dynacast, Ryobi
- Endurance Technologies
- Gibbs Die Casting
- Impro, Zetwerk
- Martinrea International, Inc
- Regensburger Druckgusswerk Wolf GmbH
- Ryobi
- Sunrise Metal
- Zetwerk
- Zollern GmbH
Automotive Casting Industry News
- In April 2024, Endurance Technologies Limited announced its approval for capacity expansions in aluminum die casting and machining of automotive components. The company plans to install state-of-the-art machines, focusing on producing machined clutch and transmission housings for four-wheelers. These additions will be integrated into their current manufacturing facilities located at plot nos. B-1/2 and B-1/3 in Chakan, Dist.
- In May 2024, Ryobi Die Casting initiated a $50 million capital investment program at its Irapuato, Mexico aluminum die-casting plant. The move aims to bolster capacity, gearing up for the projected surge in demand for electric vehicle components.
- In October 2023, CFS Foundry, a leader in high-precision casting, announced significant advancements in investment casting and die casting. Using advanced materials like stainless steel, nickel-based alloys, aluminum, and zinc, the company aims to set new standards in the automotive, food machinery, marine hardware, agricultural machinery, and glass fittings markets.
The automotive casting market research report includes in-depth coverage of the industry, with estimates & forecast in terms of revenue (USD Billion) (Kilo tons) from 2021 to 2032, for the following segments:
Click here to Buy Section of this Report
Market, By Vehicle
- Passenger cars
- Light commercial vehicles
- Heavy commercial vehicles
- Two wheelers
Market, By Material
- Iron
- Steel
- Aluminum
- Others
Market, By Process
- Sand casting
- Die casting
- Investment casting
- Others
Market, By Application
- Engine
- Transmission and suspension
- Brakes and wheels
- Others
Market, By Distribution channel
- OEM
- Aftermarket
The above information is provided for the following regions and countries:
- North America
- U.S.
- Canada
- Europe
- Germany
- UK
- France
- Italy
- Spain
- Rest of Europe
- Asia Pacific
- China
- Japan
- India
- South Korea
- Australia
- Malaysia
- Indonesia
- Rest of Asia Pacific
- Latin America
- Brazil
- Mexico
- Rest of Latin America
- MEA
- Saudi Arabia
- UAE
- South Africa
- Rest of MEA
Frequently Asked Questions (FAQ) :